For the over 400 years, hardwood flooring has graced homes across the world. Starting in France during the Baroque Era and popular among colonists in North America, it has remained a classic, sought-after floor solution due to its timeless style and durable nature. Making hardwood flooring is not as straightforward as just simply chopping down a tree and laying it down. If you’ve ever examined your hardwood floors and wondered how they got there, wonder no more! Let’s break down exactly how hardwood flooring is made.
It is important to note that throughout the years, hardwood has evolved into two main types: solid and engineered. Solid hardwood is made of a thick slab of wood from one singular type of tree. The tree species varies from oak to walnut to maple, etc. Engineered hardwood is made of a thin top layer of hardwood to give off the appearance of classic wood flooring, with a thin layer of plywood underneath. While these two options look almost identical and require the same level of care and cleaning, here are a few important distinctions between solid and engineered hardwood.
- Solid hardwood:
- Lasts 30 to 100 years
- Is more expensive per square foot
- Can be sanded up to ten times, depending on warranty
- Has thicker planks
- Is more difficult to install
- Has a larger variety of colors
- Engineered hardwood:
- Lasts 20 to 40 years
- Is less expensive per square foot
- Can be sanded from one to three times depending upon the veneer thickness
- Has planks that are bigger both in length and width
- Is easier to install
- Is more water-resistant and, depending on manufacturing, can be waterproof
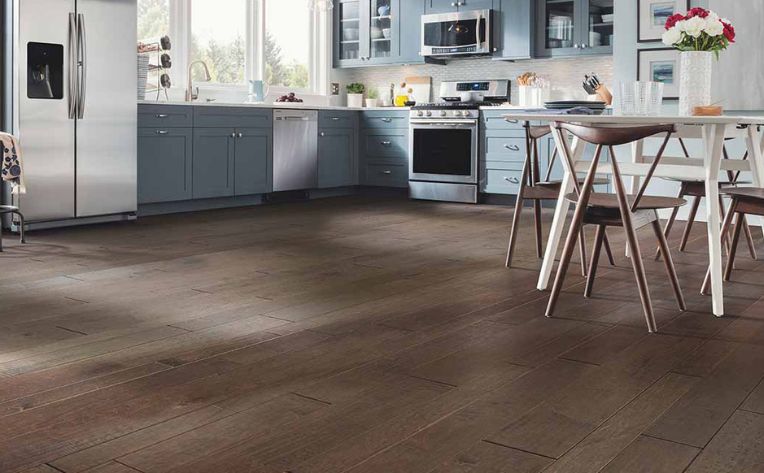
Another important distinction is how these hardwood types are made. Solid hardwood comes from one type of tree and is created through the following process:
- After a tree is cut down into logs, it is closely examined for its quality, which is determined by how tight the grain is and how many knots are in it. The tighter the grain and the fewer the knots, the better.
- The logs that meet the qualifications of quality hardwood are then converted into planks through one of these three cutting methods:
- Flat or plain sawn is the most common and has the most variations compared to the other methods.
- The quarter sawn method, as you may expect, cuts the wood into quarters and, from there, cuts the wood into strips.
- The rift sawn method is the most expensive method and produces the most durable hardwood floors. Like the quarter sawn method, it cuts the wood into different angles before cutting the wood into strips; however, it is cut from different angles than the method mentioned above.
- Regardless of the method chosen, the planks are examined, and whichever ones make the cut (pun intended) are smoothed to remove any saw marks and leveled.
- To have the wood fit together edge to edge, tongues and grooves are cut into the edges of the wood planks. From there, the wooden plank may go through a distressing process by hand or machine.
- Finally, the hardwood is given a protective finish by either a staining or sealing process, which can occur before or after it is installed.
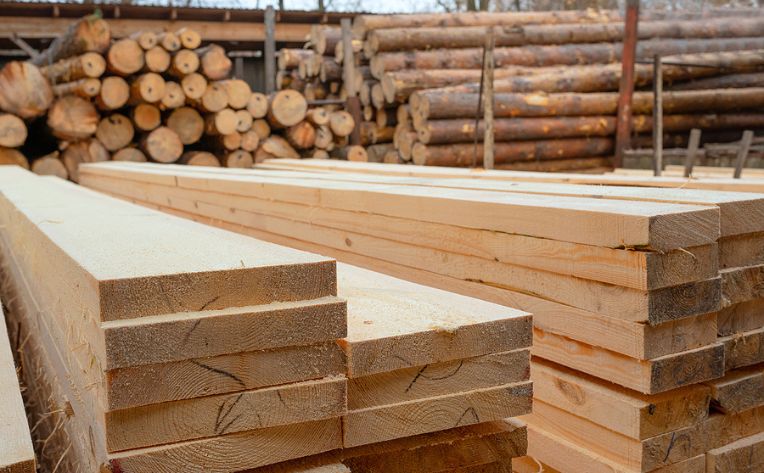
Since engineered hardwood is made up of both a thin layer of hardwood and plywood, two production processes are necessary to develop this flooring option. The thicker both layers are, the more expensive and durable the flooring becomes. Since there are multiple types of engineered hardwood from MDF to HDF to solid core and more, the processes vary from type to type. In this instance, we will be discussing how ply-core engineered hardwood is made:
- The plywood underneath the thin hardwood layer is made up of wood piles that are glued together and stacked in the opposite direction to create stability. The final result of the wood that is piled, stacked, and glued is called the core board. At the same time, another process occurs to create the top, visible, thin hardwood layer. There are three different kinds of cutting methods:
- Dry-solid sawn is the most expensive method, as it achieves the tightest grain and looks as well as acts the most like solid wood. During this process, wood is slowly dried out with low humidity, which keeps the moisture inside of the wood and, in turn, reduces the risk of the edges of plank curving up (this undesired risk is called cupping).
- Rotary-peel occurs when the wood from the log is scraped and pressed flat after the log has been boiled for a long period of time. The grain closely resembles plywood, and the planks developed from this method may face issues with cupping.
- Sliced-peel method also boils the log; however, the wood is cut from the end of the log and pressed until a veneer is created.
- Once the core board and hardwood layers are both created, they are glued together.
- Following that, the edges are cut to create tongue and grooves for a glue-less click-and-lock system to create an edge-to-edge look.
- Like solid hardwood, the layer of wood in engineered hardwood flooring can go through an optional distressing process, which is more expensive but achieves the antique aesthetic. It is also given a protective finish like solid hardwood through a staining or sealing process.
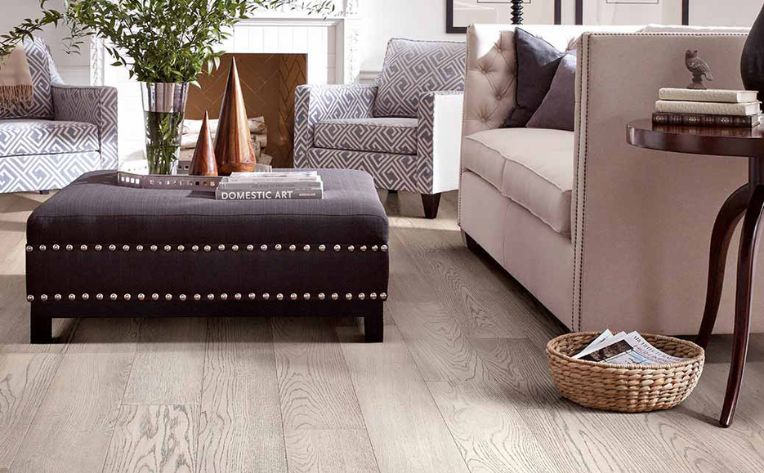
To say the least, the process of creating hardwood has come a long way since the 1600s, and in turn, our flooring today can withstand the test of time not only in its classic look but also in its lifespan. You can read more about how hardwood is made and its different styles or speak to an expert by visiting your local Flooring America.